A building at the heart of Bluefactory
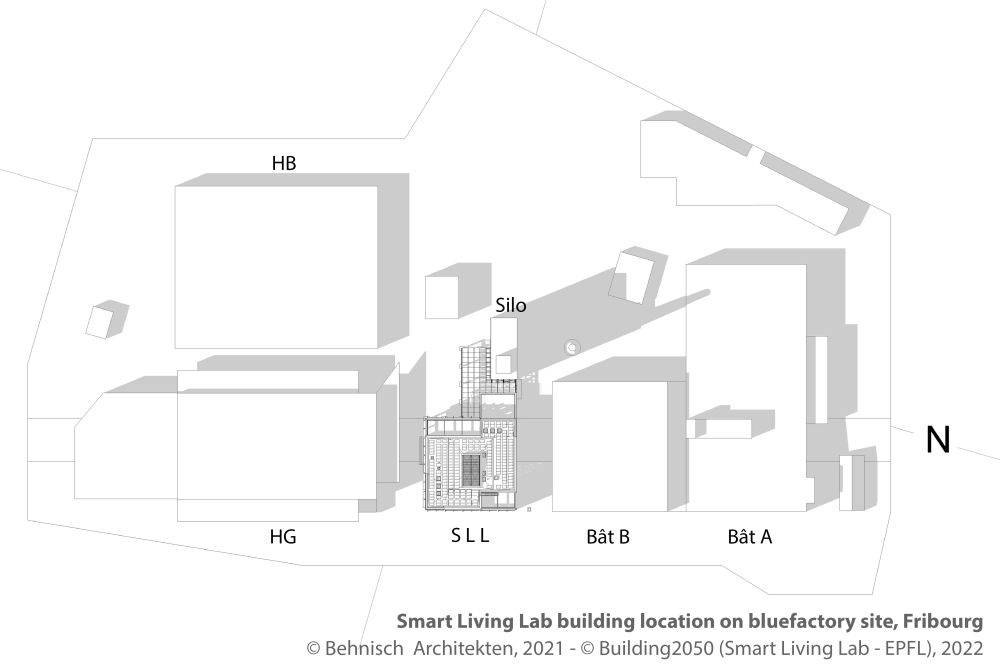
The construction project, which benefits from Canton of Fribourg funding, was jointly developed by the Contracting authority BFF SA and the Smart Living Lab team. Once completed in 2025, the new facility in the heart of the Bluefactory site will provide laboratories, offices, and workstations for staff from EPFL, the School of Engineering and Architecture of Fribourg, and the University of Fribourg. In 2018, the project got off the ground with the launch of a 'Parallel Studies Mandate' (MEP), an innovative collaborative design process and investigated by the authorities in 2021.
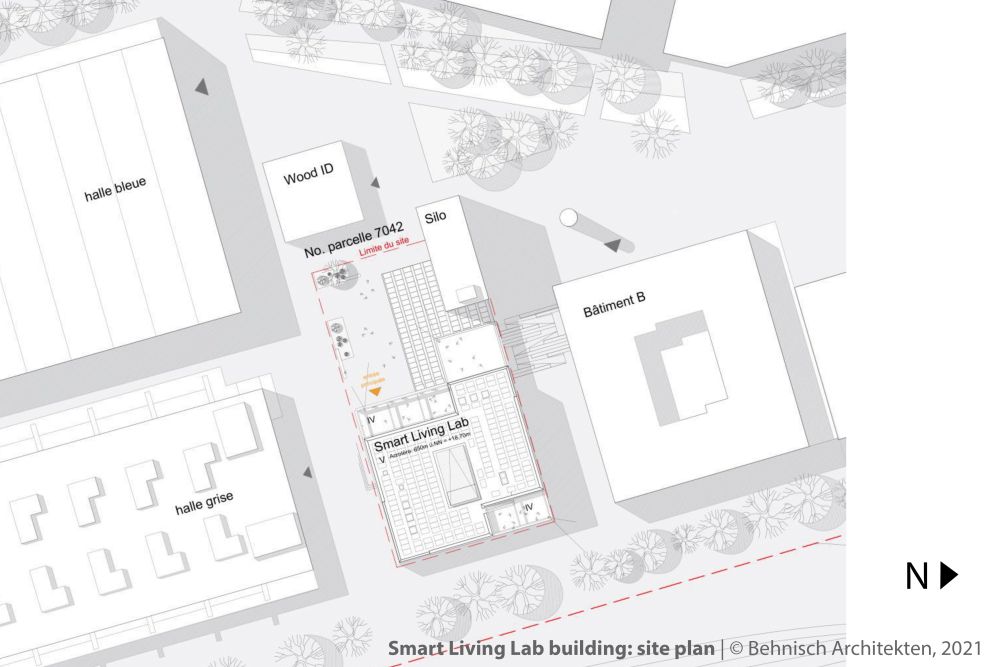
The groundbreaking Smart Living Lab Building is not the only Bluefactory construction project.
Building B
Construction is already under way on Building B, on the north side of the Smart Living Lab. Scheduled to open in 2024, it will house offices, laboratories, prototyping spaces, conference rooms and restaurants.
Silo
The canton of Fribourg Culture Heritage Service has designated the former grain silo as a structure of particular architectural and historic interest. In 2023, an design competition was launched to renovate this listed building.
Wood-iD
This modular building was constructed in 2021 using an innovative prefabrication process which will also make it possible to dismantle the structure at the end of its 5-year life cycle. Start-ups are the primary occupants of Wood-iD.
Blue Hall
This former industrial storage depot has been converted into offices and laboratories for companies and research centers. One of its current occupants is the Smart Living Lab.
Grey Hall
The canton of Fribourg Culture Heritage Service has designated the Grey Hall as a structure of particular architectural and historic interest. Once redevelopment work is completed, this listed building, which is located on the south side of the Smart Living Lab, will be home to the HEIA-FR architecture department, as well as the heat pumps that will power the Bluefactory's low-temperature district heating grid.
Annex 2
This building was demolished in early 2022 to make way for the Smart Living Lab building.
Utility corridor
This underground passage will connect several buildings and accommodate all the utilities they need.
Geothermal probes
Geothermal probes will supply the Bluefactory district's low-temperature district heating grid. Several probes will be placed under the site's buildings, including the Smart Living Lab, which will help to maintain an area of open ground. This outdoor space will be landscaped and will include vegetation and wetlands.
Vermicomposting
A vermicomposting facility located between the Smart Living Lab building and Building B will treat all Bluefactory wastewater on site and convert it into fertilizer.